本篇文章給大家談談精益生產訂單處理流程,以及精益生產訂單處理流程圖片對應的知識點,希望對各位有所幫助,不要忘了收藏本站喔。
今天給各位分享精益生產訂單處理流程的知識,其中也會對精益生產訂單處理流程圖片進行解釋,如果能碰巧解決你現在面臨的問題,別忘了關注本站,現在開始吧!
本文目錄一覽:
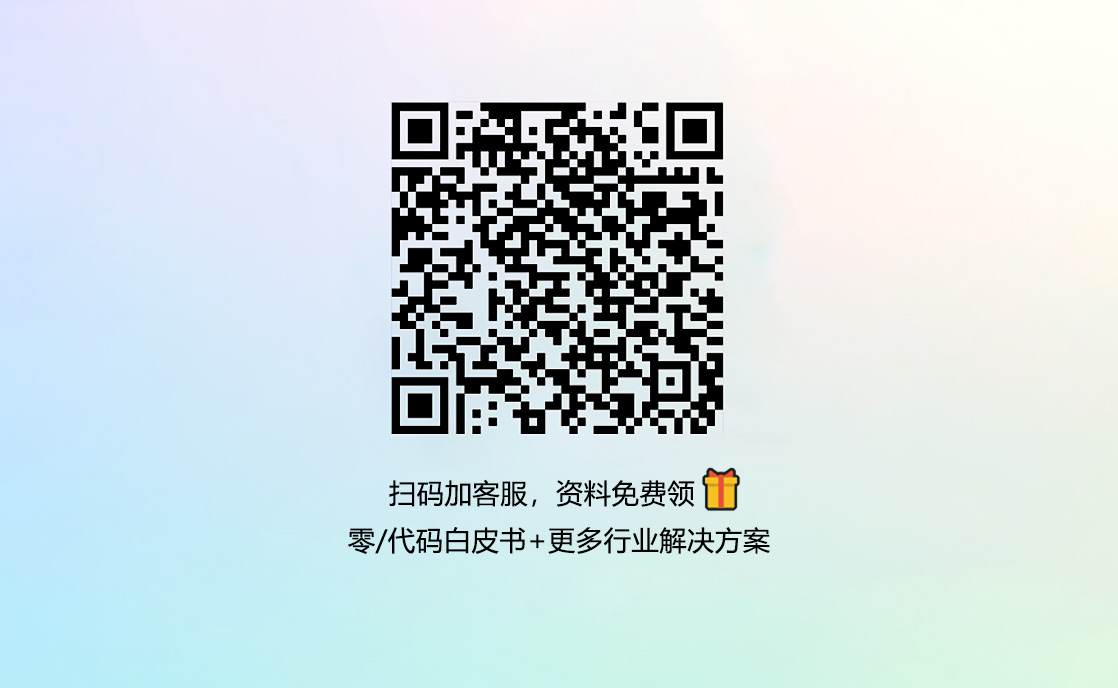
精益生產怎么做?
精益生產怎么做
精益生產訂單處理流程?
天行健咨詢公司在這里提供一個推進精益生產
精益生產訂單處理流程的流程步驟供大家參考
精益生產訂單處理流程,但具體的推行步驟是必須根據企業實際情況來制定針對性的推行方案的。盲目生搬硬套,不根據企業實際情況去推行精益生產,失敗是理所當然的。
步驟一:提高思想認識,強化組織領導
實施精益生產發揮員工的作用是關鍵。加強全員的精益管理意識的教育和培訓,參加的人員要實現從管理層的老總、副總,到操作層的普通工人。培訓內容包括:競爭的情況、浪費觀念、拉動生產、5S、團隊改善、全員的設備管理、質量管理等內容,促進企業全體人員轉變思想觀念,增強推行精益生產方式的自覺性和主動性。成立推行精益生產方式的專項領導及推行機構,由總經理擔任負責人,相關業務管理部門主管參加,明確職責和任務,制定精益生產工作計劃,推動精益生產方式在企業的落實。
步驟二:成立項目領導和項目推行小組
這一步是要建立一個精益生產組織。這也是很多企業實施精益生產時必經的一步,有的企業把這個小組叫“精益生產委員會”,有的叫“改善組織”。一般來說,總經理應是精益組織的負責人,有些企業也把工廠負責的副總經理列為負責人,組織應包括生產管理部門、制造部門、生產技術部門、品質部門的等相關部門的主管,要確立負責人的改善職責。
步驟三:建立示范線,確定管理樣板
在實施精益生產方式3至6個月后,當5S獲取初步成效時,應選擇一個生產線作為示范推進持續改善。改善內容應盡力運用好精益工具,同時注意選擇那種流水作業的生產線,明確改善之前所處的狀態,如:成品和零件的清單、現狀物和情報的流程圖、各工程的時間調查、生產線邊上的庫存情況調查以及送貨的頻率與數量等情況。改善必須堅持循序漸進的原則,落實責任人,注意運用好頭腦風暴方式進行集中全體人員的智慧。對改善情況要及時進行發布,從而確保改進工作
同步實施、順暢合作。同時改善示范線負責人,還要在每天確認改善進度。
步驟四:現場改善,從5S開始
5S管理(整理、整頓、清掃、清潔、素養)。實施精益生產方式,首先必須從改善現場的環境開始,經過整理來清理不要的物品,減少對空間占用
精益生產訂單處理流程;經過整頓來使現場物品有序地擺放;經過清掃,使現場保持干凈,使設備及時保養;經過檢查和整改,使員工形成好習慣,以保持良好的現場環境,從而提高企業的生產效率及產品質量。最終通過5S活動,實現現場的有序化管理,并減少浪費的現象,增強全員生產和管理的改善意識。
精益生產從5S管理開始,一方面,在5S的活動下,讓現場走向有序化,減少一些比較顯現的浪費現象;另一方面,通過領導的參與,讓員工明白管理層對改善的決心,提高全員的改善意識。
步驟五:繪制生產價值的流程圖
在繪制價值流程圖時,用方框表示各個生產工藝,用三角框來表示工藝間在制品的庫存情況,而用不同的圖標標識出不同物流與信息流,信息系統與生產工藝間的連接折線說明信息系統在對生產工藝排序等;并通過生產過程中增值部分與不增值部分的標注,以便減少生產浪費現象。生產價值的流程圖主要是用來進行物流及信息流描述的一種方法。完成當前價值的流程圖繪制之后,就能夠描繪出精益生產的遠景圖。
步驟六:開展改進研討會
精益遠景圖必須付諸實施,否則規劃得再巧妙的圖表也只是廢紙一張。實施計劃中包括什么(What),什么時候(When)和誰來負責(Who),并且在實施過程中設立評審節點。這樣,全體員工都參與到全員生產性維護系統中。
在價值流程圖、精益遠景圖的指導下,流程上的各個獨立的改善項目被賦予了新的意義,使員工十分明確實施該項目的意義。
企業實施精益生產管理有哪幾大步驟
1、第一步,全面提升現場管理水平
通過實施5S管理改變作業現場面貌創造有序的工作環境,減少各種尋找的時間,提高效率,達到全體員工遵守規定的習慣和不斷尋求改善的職業素養。
精益生產管理
2、第二步,實施
同步化生產
同步各工序間的生產,盡量使工序間在制品數量維持最少水平。即前工序的加工一結束,產品應該立即轉到下一工序。通過在設備、人員、生產線進行相應如下布置,將有助于同步生產的達成。
①單件流;
②按工藝順序布置設備,盡可能達成裝備流水線化;
③實行節拍生產;
④按人體工學原理布置作業區域;
⑤培養多能工,實現少人化;
⑥盡可能使用小型設備便于再布置;按“U”形布置生產線;實施標準化作業。
3、第三步,實施均衡生產
減少原材料、在制品與成品等各種存貨。在精益思想里生產一件產品要花多少時間,不是由機器或人員作業速度決定的,而是由市場需求來決定的。所以在精益生產方式中只有“多長時間生產出一件產品才好”,這就節拍生產。假如一天市場需求量是100個,工作時間是300分鐘,那么就應該使生產線每隔3分鐘生產一個產品,使每一個環節都按均衡化生產的需求來安排各自的節拍,而不是連續做得越快越好。
4、第四步,實施準時化采購與準時化物流
精益思想必須向企業制造鏈的上下游進行延伸,對整個供應鏈及物流體系進行精益化布局,從而使企業的每一環節都能發揮出最大的效益。在精益思想里,為了消除采購過程的浪費,主張減少合格供應商的數量,并建立與供應商長期的、互利的合作關系。這樣才能建立互信與信息
共享,實現快速溝通,解決品質問題,保證準時供貨。在物流過程中,主張采用先進的交通工具、通訊手段和信息技術,同時在企業的組織結構上,盡可能減少縱向層級,打破部門壁壘,依靠技術手段提高效率,滿足
客戶需求。
5、第五步,進行看板管理
為了實施“拉動式”生產,實現同步化生產,通常采用“看板”管理工具。為了有效實施看板管理,有時需要對設備進行重新排列布置,做到各工序所有需要的零部件都只從前工序獲取,在整個生產過程中物流要有明確的、固定的移動路線。將物流與信息流區分為工序之間和工序內的物流與信息流,分別由“傳送看板”和“生產看板”進行控制。所以精益生產方式中所指的看板是銜接上下工序工作的指令和信息紐帶,這是與普通看板的區別所在。進行看板管理需要遵守以下5個使用規則:
①沒有看板不能生產,物資不能流轉;
②看板只能來自后道工序,前工序只能生產后工序取走的部分;
③前工序按收到看板的順序進行生產;
④看板必須與實物在一起;
⑤不能把不良品傳遞給后工序。
6、第六步,實施柔性化生產組織管理
柔性化生產組織主要包括兩方面:第一,產量的柔性;第二,時間的柔性。要實現生產的柔性化,通常需要建立整個企業系統能力的柔性,一般在制造企業中,主要實施內容為:
①研發部門的模塊化設計
設計產品時就要考慮由若干個模塊組成一個產品的可能。這將有利于各個單元可以獨立拆裝,獨立升級改進,降低生產與維修的難度。
②生產制造部門的裝備線與人員的柔性
柔性生產要求實行細胞式生產方式及固定變動并存的生產方式,推車式柔性生產線等,以不同的生產方式組合以確保既能滿足生產效率最佳化又能滿足柔性變動能力的要求。
③企業所有組織工作的提速
通過業務流程的精益化和有效的授權管理,縮短任何業務在任何部門的辦理、決策等過程所用時間。
④建立生產組織結構的柔性
在推行精益生產的企業,除了常設部門外,經常還要
設置跨部門的臨時組織,成立更具靈活性、更能適應市場需求項目推進小組,統一協調推進精細化管理的實施。

精益生產處理問題的流程DMIAC是指
DMAIC分別是指Define, Measure, Analyze, Improve 和 Control。是來自六西格瑪的一種管理模型,很類似于質量管理的PDCA,計劃管理的PDSP。
1、五大步驟分別是:界定、測量、分析、改進、控制。
2、界定:需要用清晰的,可量度的語言將問題進行準確描述和界定(比如說符合SMART原則等),這個階段會制定任務書,將任務描述,整改的期限,整改前后的效果等一系列數據描述出來。
3、測量:y=f(x),簡單的來說就是一個結果是N個因素作用的結果,因此必須清晰的找到運作系統/流程f(x)中的影響因素x。
4、分析:利用各種分析工具,直方圖、柏拉圖等將能夠查找到的因素進行分析;
5、改進:針對找到的問題進行針對性的優化和改進,從而讓運作系統能夠更好的運作
6、控制:對改進措施落地的檢查,防止再發生的預防機制等
精益生產價值流改善步驟有哪些?
1、選定區域(定義價值流范圍)
2、繪制選定區域的價值流圖(Value Stream Mapping)-- 團隊了解現狀 ,采用現場實際數據,不要用理論或系統中的數據
3、定義未來3~5年的遠景目標(Value Stream Design) -- 定義未來的發展方向,使用綠地原則。
4、比較現狀和遠景目標,找出改善點。
5、根據實際情況定出大的改善步驟:把所有的改善點分配到各個年份,以達到遠景目標。
6、根據已經定義好的大的改善步驟,仔細規劃第二年要做的事情,列出一個task list,并定義好每一項任務的負責人和完成日期。
7、最后用PDCA的工具來進行任務的追蹤就可以了。
對于VSM/VSD工具的使用,可以參考《學習觀察》這本書。
歡迎追問,祝你成功!
關于精益生產訂單處理流程和精益生產訂單處理流程圖片的介紹到此就結束了,不知道你從中找到你需要的信息了嗎 ?如果你還想了解更多這方面的信息,記得收藏關注本站。
精益生產訂單處理流程的介紹就聊到這里吧,感謝你花時間閱讀本站內容,更多關于精益生產訂單處理流程圖片、精益生產訂單處理流程的信息別忘了在本站進行查找喔。
版權聲明:本文內容由網絡用戶投稿,版權歸原作者所有,本站不擁有其著作權,亦不承擔相應法律責任。如果您發現本站中有涉嫌抄襲或描述失實的內容,請聯系我們jiasou666@gmail.com 處理,核實后本網站將在24小時內刪除侵權內容。
版權聲明:本文內容由網絡用戶投稿,版權歸原作者所有,本站不擁有其著作權,亦不承擔相應法律責任。如果您發現本站中有涉嫌抄襲或描述失實的內容,請聯系我們jiasou666@gmail.com 處理,核實后本網站將在24小時內刪除侵權內容。